EMISSIONS REDUCTION INITIATIVES
A focus on innovation and cross-company collaboration enabled us to chart a clear and defined path towards achieving our goal of reducing our Scope 1 & 2 GHG emissions intensity by 50% from 2019 levels by 2030. We are committed to making real and meaningful emissions intensity reductions in our operations by doing what we do best – innovating to drive efficiencies and unlock future opportunities.
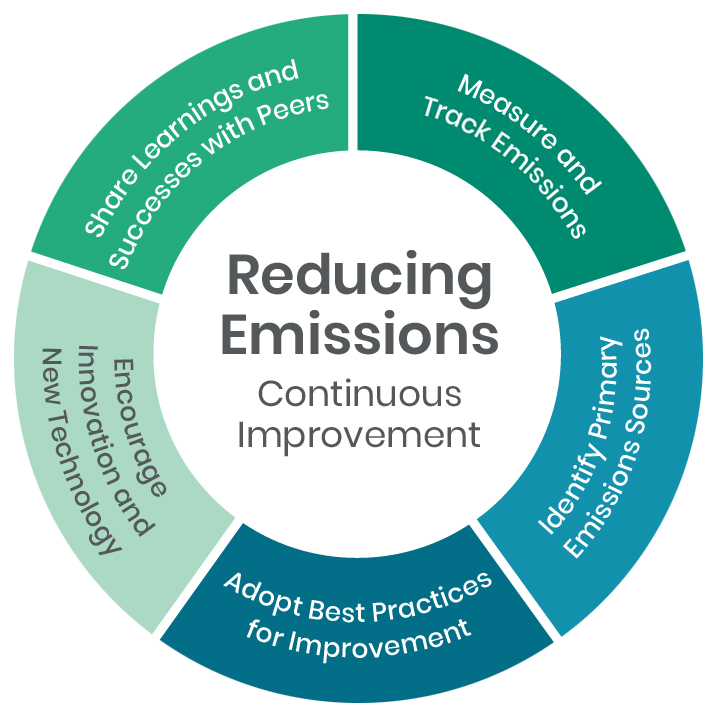
Centralized Planning to Drive Innovation
We drive continuous improvement throughout our organization by bringing together proven experts from key parts of our operations and across our operating areas to form our Chiefs teams. Our newly formed Chief Digital Office team is tasked with driving digital innovation and transformation throughout our organization by reviewing work processes and focusing on projects that impact profitability and drive further efficiencies. Our Chief Engineering Organization, which includes our Emissions Performance Group, facilitates a multi-basin approach to reducing costs, solving complex challenges, developing new products, sharing emerging technology across disciplines and driving strategic progress towards achieving our Scope 1 & 2 GHG emissions intensity reduction target.
Realized
Initiatives
Technology and processes that are being deployed at scale in our operations
High-pressure flare reductions
Ovintiv continues to work towards eliminating routine flaring in our operations. Through our focus on efficiency and continuous improvement, we actively manage our flaring performance and expect that compliance with new regulations will further reduce flaring in our operations.
To better understand where and when flaring occurs in our operations, we created an internal dashboard to examine flaring volumes. We use the data to generate plans to reduce flaring volumes through a variety of innovative approaches, including novel midstream solutions. Examples include:
- Installing secondary gas takeaway connections at some sites to avoid flaring during infrastructure upsets and working closely with our midstream service providers to reduce downtime.
- Testing on-site data computing solutions that use excess gas resulting from midstream constraints, which would have been flared, to generate electricity for powering mobile data centers.
- Utilizing mobile compressed natural gas generation facilities to complete a virtual pipeline network, connecting producing locations to the midstream pipeline network via trucking solutions with specialized trailer systems.
- Piloting numerous closed-loop gas capture projects to further minimize flaring. Closed-loop gas capture involves temporarily re-injecting excess natural gas into a wellbore during midstream upsets, which would otherwise be flared. This gas is then recovered upon the restoration of midstream service.
Tracking fired-burner runtime
Natural gas-fired burners are used in the surface facility process to meet sales specifications before oil flows into the sales pipe. We have made a focused effort to gather operational data on the burners in our Anadarko and Permian operations. In addition to increasing the accuracy of our GHG reporting, this data has enabled operational synergies such as optimizing burner fuel usage and increasing production reliability.
Finding alternatives in wellsite facility design
Ovintiv has developed innovative wellsite designs that are being routinely implemented across our operations and incorporate numerous technologies and practices that reduce emissions, including:
- Eliminating high-emitting equipment such as line heaters
- Reducing our pneumatic chemical injection pumps
- Finding alternatives for natural gas driven pneumatics (e.g., electric actuation, instrument air or liquid nitrogen systems)
In the U.S., our new well-pad facilities use instrument air powered pneumatic valves in place of natural gas-powered pneumatics. We employ a fit-for-purpose design that allows for alignment and synergies between asset areas. In Texas, we have also developed a design on our Permian wellsites that includes zero-bleed pneumatic devices and electrically operated control valves and chemical pumps.
In Canada, the current design involves a closed system that captures and combusts methane from gas-driven pneumatic controllers and pumps that would otherwise vent to atmosphere. Field tested in 2020, the non-venting wellsite design has subsequently been deployed at new wellsites in British Columbia and Alberta. We are also installing nitrogen systems that replace natural gas as the drive gas, avoiding potential methane emissions. These units have been installed on over 70 sites in Alberta and British Columbia and are now standard design for new wells in Canada. This technology was also featured at COP28 by the Government of Canada as one of Canada’s innovative, home-grown technology solutions to methane emissions.
Capturing and selling tank vapor
To reach sales specifications at our well pad U.S. facilities, oil must be stabilized at low pressures (close to atmospheric levels) and stored in tanks. In the past, it has been difficult to capture the vapors from the last stage of pressure drop, therefore, the typical protocol is to burn the vapors in a low-pressure flare. To further minimize our venting and flaring, we applied an innovative approach to tank and closed vent system design and are now capturing those emissions using vapor recovery units (VRUs). The VRUs capture the emissions and compress them into the sales line, which also generates revenue. This technology will result in an approximately 80% reduction in GHG emissions associated with low-pressure flaring per facility. While this has become a standard element in our new U.S. located facilities, we are also evaluating the potential to upgrade tanks on our legacy assets to achieve similar results.
Powering production with hydroelectricity
In British Columbia, Canada, the electrical grid is powered by hydroelectricity rather than natural gas or coal. The majority of processing plants that Ovintiv operates in the Montney field, including the Saturn, Sunrise and Tower gas plants, are tied into the electrical grid in British Columbia. These plants avoid up to 860,000 tons of carbon dioxide equivalent emissions annually, comparable to the emissions from 184,000 vehicles per year. Electrification has the added benefit of reducing operational noise compared to non-electric facilities. We continue to leverage electric power on new equipment and are evaluating converting existing infrastructure where appropriate.
In 2024, our partnership with a midstream company resulted in the construction of a transmission line, which enabled the midstream company to electrify their processing plant in British Columbia avoiding approximately 80,000 tons of CO2e/year. The electrification also allowed Ovintiv to increase our power capacity at other plants and make electricity available for future infrastructure projects.
Utilizing natural gas technology in our completions operations
As part of our focus on driving efficiency across our business, we have integrated a natural gas-powered frac fleet in our Canadian operations in place of the traditional diesel-powered fleet. This innovative technology has driven down emissions on-site, with a greater than 20% reduction in completions emissions per well completed, reducing diesel consumption by more than four million gallons in 2024. It also has a much smaller physical footprint; a pad that normally required 18 diesel pumps now uses eight high-powered natural gas pumps. This decrease in equipment and activity has also resulted in positive safety outcomes, a foundational value integrated in our approach to all work.
After exploring ways to expand similar technology in our U.S. operations, in mid-2023 we began utilizing electric fleet technology in our Permian operations. The electric fleet, which can be powered by the grid or through natural gas-powered generators, is being integrated with our innovative trimul-frac technique to gain efficiency while driving down diesel usage and lowering the emissions of our Permian fleet.
In late 2023, we also utilized a natural gas-powered frac fleet in our Anadarko operations, further driving down our diesel consumption.
Upgrading engines for lower methane emissions
Ovintiv began upgrading our fleet of natural gas-driven compressor engines to a lower emissions alternative in our Canadian operations in 2022 and have since upgraded 12 engines, replacing a total of 18,000 horsepower at five compressor sites in British Columbia. These new engines have reduced methane exhaust slip, resulting in methane emissions reductions of more than 70% at the five compressor sites since 2022. They have also increased reliability, lowered operating and maintenance costs, and have an option to increase horsepower for incremental production throughput.
In Motion Initiatives
Technology and processes that are in the early phase of development and currently being evaluated for use on a larger scale
Measuring engine load
In our Permian and Anadarko operating areas, we are testing instrumentation to measure engine load and calculate fuel consumption by incorporating engine data and manufacturer-published analytical tools. In 2024, we installed instrumentation on 35 compressor engines which will increase the accuracy of our reported GHG emissions from gas lift compressor engines and provide optimization data that will increase utilization and lead to a more efficient use of horsepower per well.
Powering drilling operations with electricity
We have trialed electrified drilling rigs in place of traditional diesel-powered generators, which resulted in lower drilling emissions per well and significantly reduced job-site noise levels. There are existing synergies in place, for example, our pad sites already use electrical power once the wells start producing. This effort required cross-team collaboration between electrical engineering, construction, production operations and our drilling team. We also worked closely with our supplier to create diesel redundancies to ensure seamless operations during utility-power upsets. We successfully drilled over 15 wells using electric drilling rigs to-date and are evaluating opportunities to expand this program going forward.
Expanding our electric-drive portfolio
In operating areas with available electricity, we are evaluating the opportunity to expand our electric-drive portfolio to include:
- Artificial lift technology (gas lift, pump jacks and jet pumps)
- Water and disposal well facilities
- Process controllers (e.g., liquid-level controllers)
- Chemical and fluid transfer pumps
- Lease automatic custody transfer units
- Vapor recovery units
We are introducing this equipment across our operating areas and will continue to evaluate opportunities for growth as electricity becomes available.
Transforming completions with innovation
We use innovative completions design to hydraulically fracture multiple wells simultaneously. By pumping down multiple wells at the same time, we can do more with the same horsepower, leading to overall energy savings and cost efficiencies. With the addition of an electrified fleet, we can further displace diesel usage and lower emissions generated by the hydraulic fracturing process. Compared to a single well frac spread, emissions can be reduced by approximately 30% by combining an electrified fleet and simultaneous well completions techniques. In 2024, we deployed this simultaneous, multi-well frac approach to 100% of our well completions in the Permian. With significant energy and cost efficiencies already achieved, we continue to explore opportunities to further optimize these innovative completions techniques.
Future Considerations
Opportunity assessments underway for future applicability in our operations
Evaluate adjacent business opportunities
We are committed to understanding potential business opportunities that complement our vision of being at the forefront of driving innovation to produce oil and natural gas – both profitably and sustainably. Industry adjacent business opportunities will be periodically reassessed in conjunction with our strategic planning initiatives.
Explore opportunities to support global emissions reduction
Ovintiv is currently exploring options, both in Canada and the U.S., to expand market access for our natural gas production via LNG exports. In 2023, we announced our partnership with Rockies LNG Partners (“Rockies”). Rockies is a group of Western Canadian natural gas producers working together to support LNG export opportunities for Canadian natural gas and is joined in a unique alliance to develop the Ksi Lisims LNG project off the west coast of British Columbia. Ovintiv’s participation in the Rockies partnership provides us the option to enter a long-term agreement to supply natural gas to the LNG facility, subject to a final investment decision on the project. It also offers the shortest shipping distance to Asian LNG markets from North America, in contrast to other LNG-producing regions.