We lead with safety
“We are resolute in our commitment to ensuring our employees and service providers go home safely every day. This starts with safety leadership, attention to serious injury prevention, understanding core safety concepts, and reinforcing a culture that prioritizes safe work always.”
Greg Givens, Chief Operating Officer
SPOTLIGHT
SAFETY COMMITMENT DAY
As part of ongoing efforts around safety improvement, Ovintiv hosted its first Safety Commitment Day in October 2024. The day provided an opportunity to reflect on the progress made with respect to safety and serious injury prevention. Members of the executive leadership team and senior leaders visited corporate and field offices to listen to staff and better understand how staff are experiencing safety at Ovintiv with the goal of gathering feedback to further improve our safety culture and reaffirming our collective commitment to protecting our people.
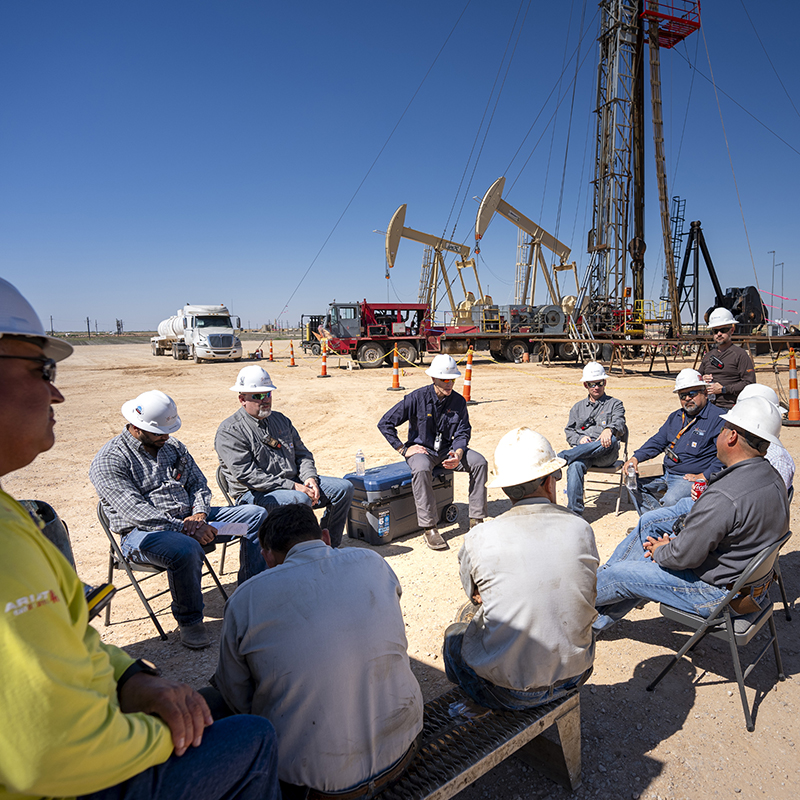
Total Recordable Injury Frequency
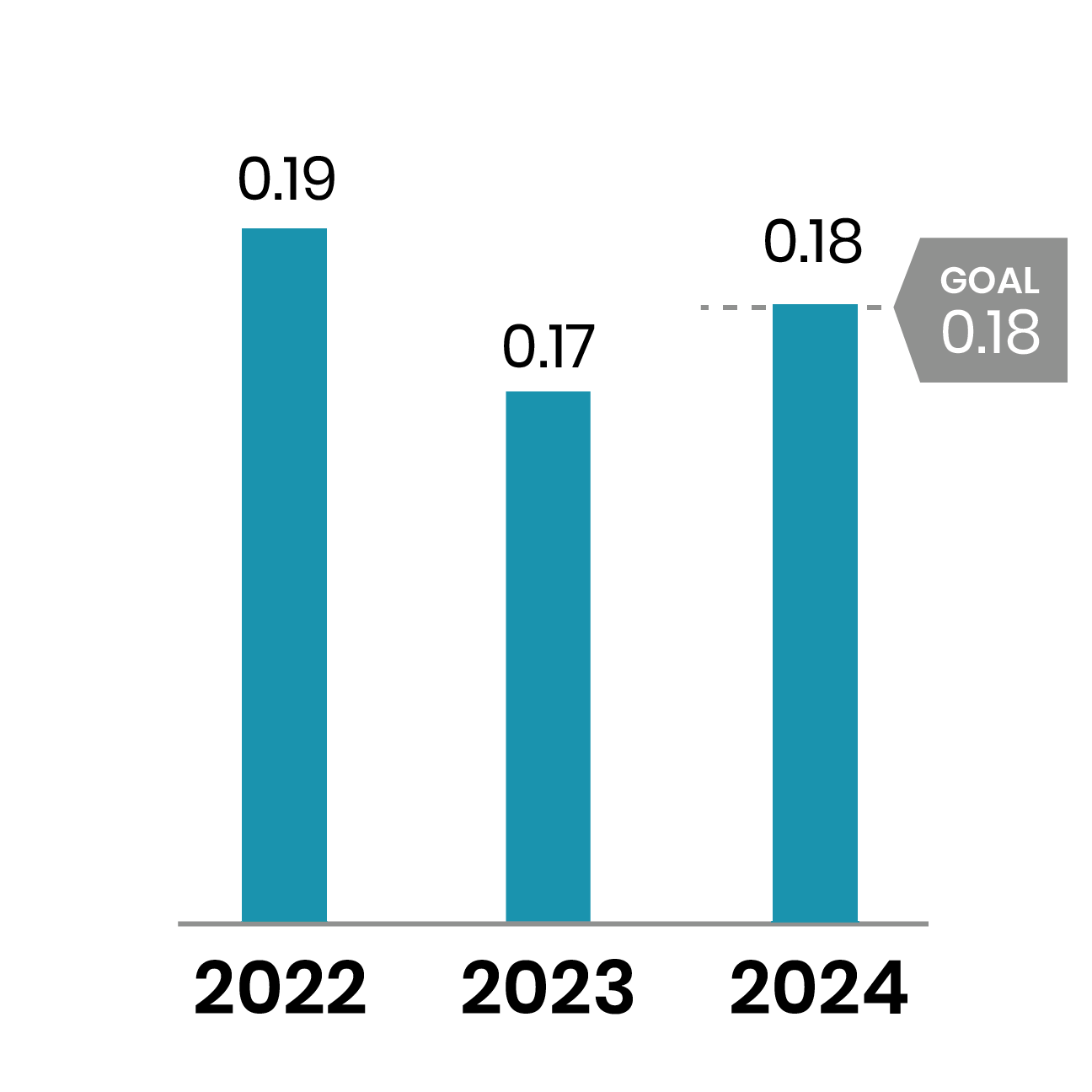
Injury
Severity*
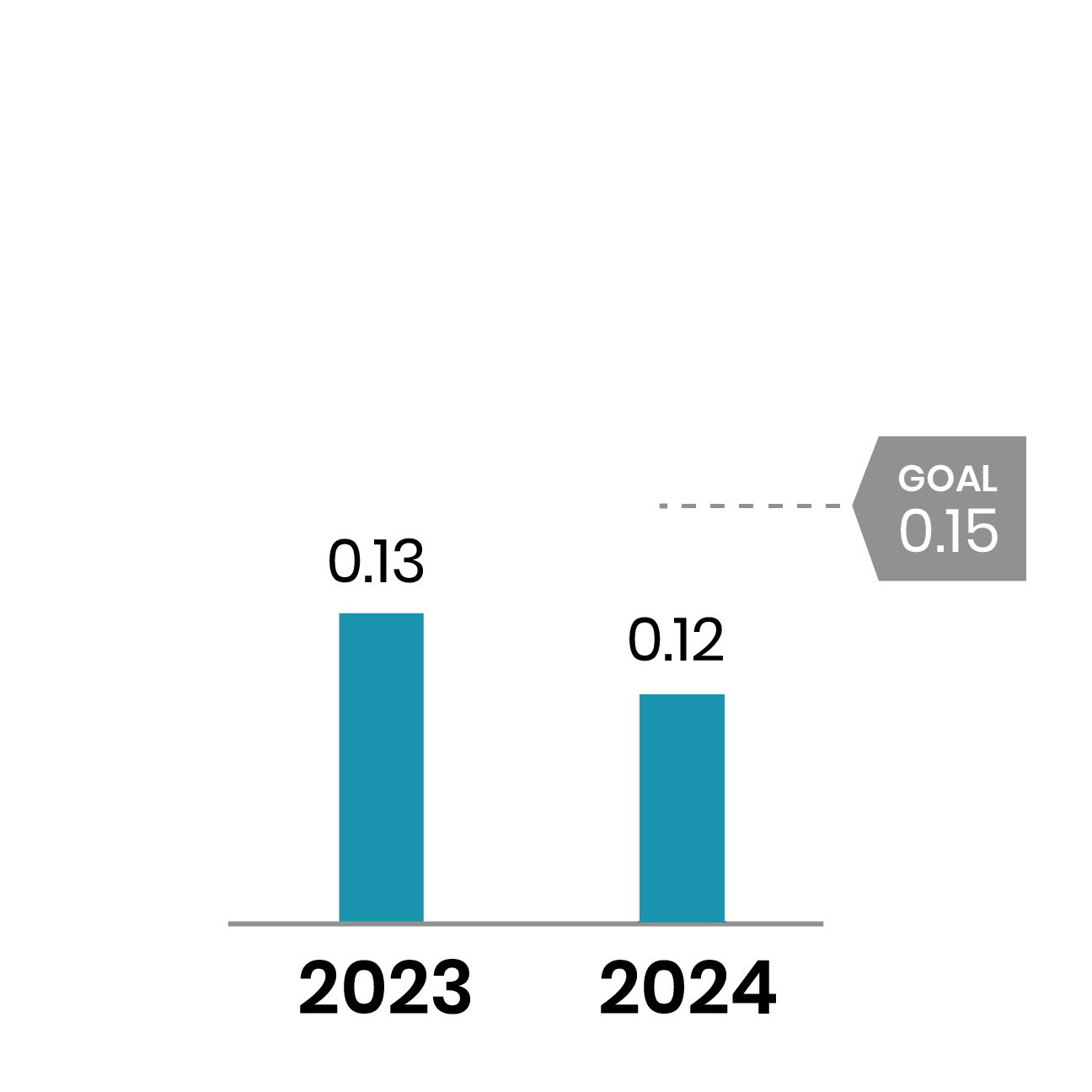
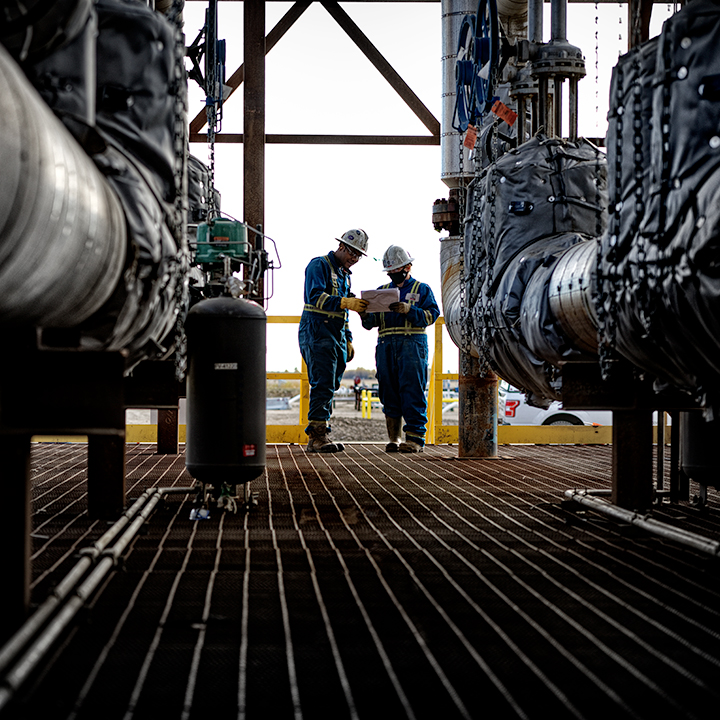
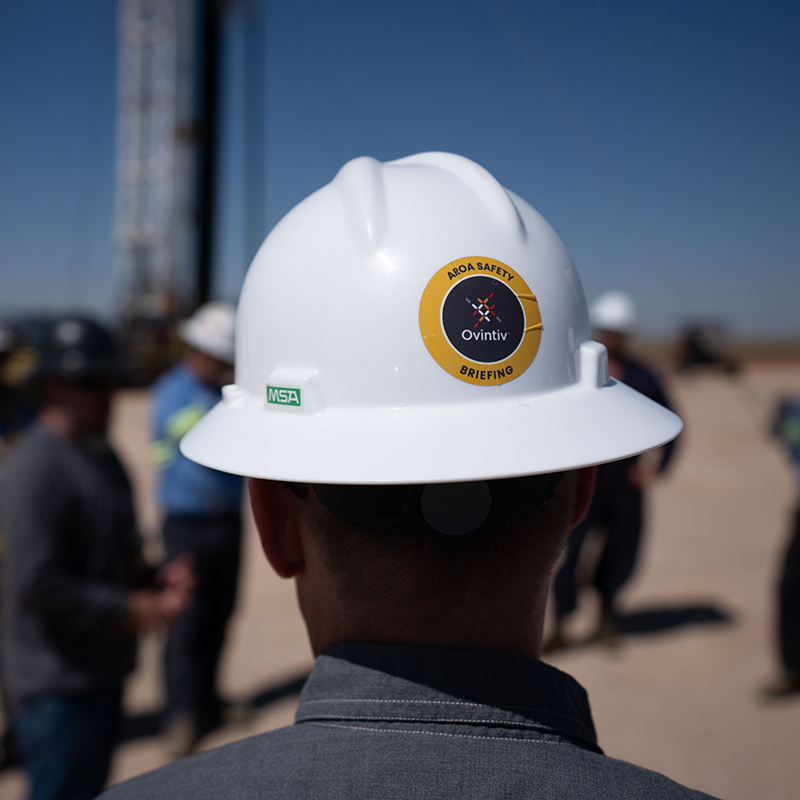
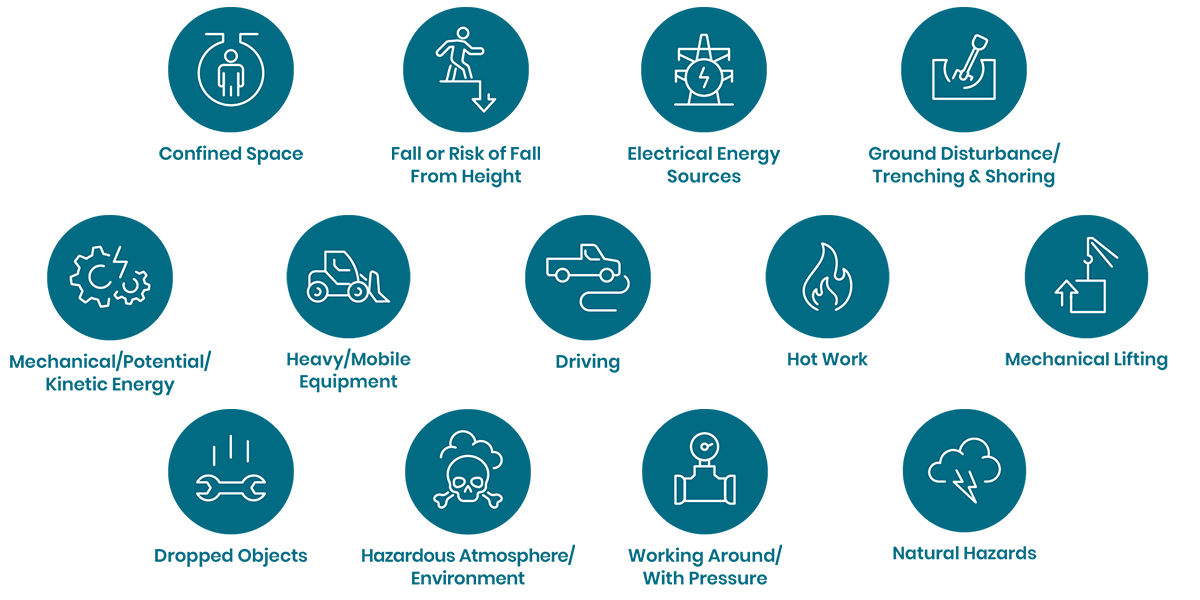
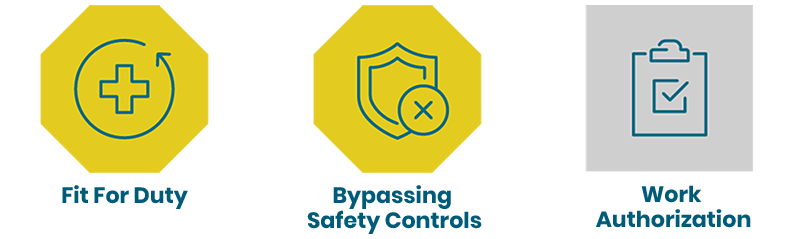
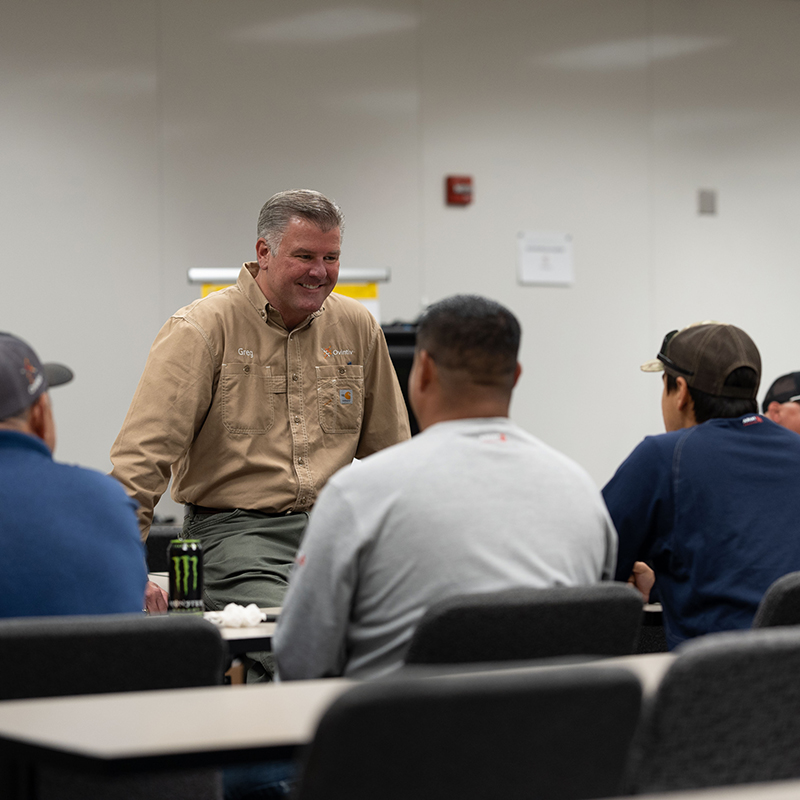
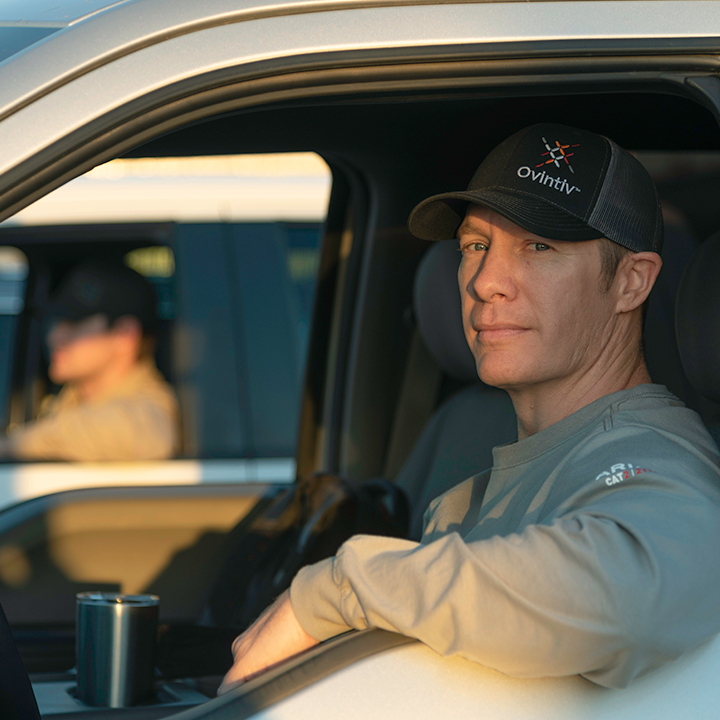
In addition to tracking these assessments to maintain supplier performance history, we use ISNetworld to further evaluate supplier safety programs and performance. ISNetworld allows Ovintiv to verify that our suppliers have acknowledged and adopted the required EH&S procedures before starting work.
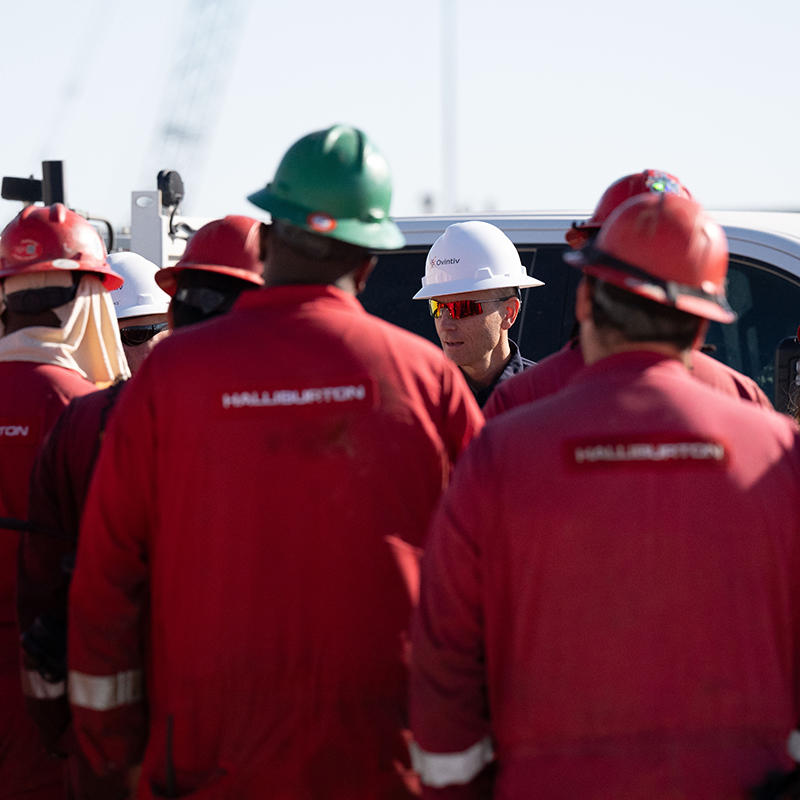
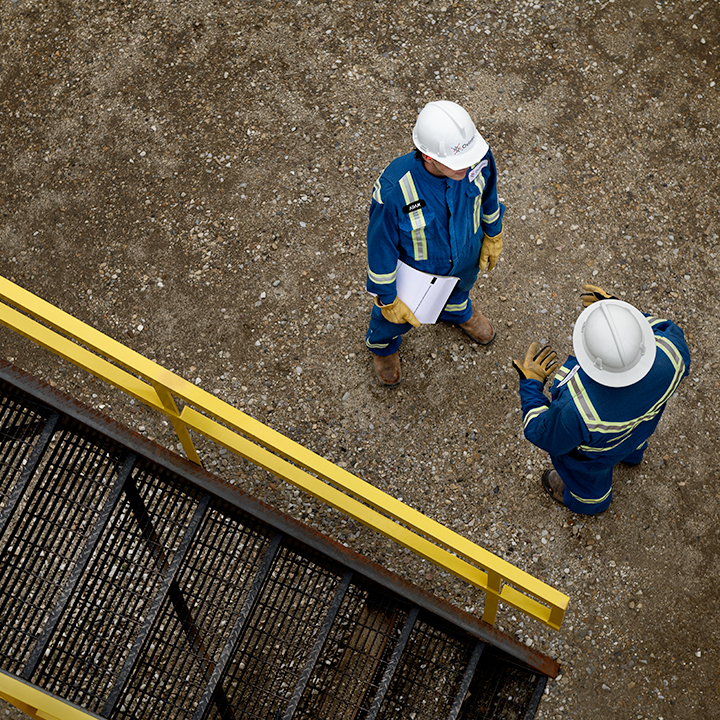